What Is CNC Milling?
CNC milling is a precision machining process where computer-controlled machines remove material from a workpiece to create complex and accurate components. Unlike other CNC processes, milling involves a rotating cutting tool that moves along multiple axes to shape the workpiece. This method allows the creation of intricate parts with tight tolerances and complex geometries.
CNC milling is especially effective for producing components with flat surfaces, slots, holes, and even intricate 3D contours. It is widely used across industries such as aerospace, automotive, medical, and automation, as it can handle a variety of materials, including mild steel, stainless steel, aluminium, brass, and plastics as well as many others.
.webp?width=4160&height=2340&name=IMG_20181017_093125%20(1).webp)
Benefits Of CNC Milling
Precision And Accuracy
CNC milling delivers exceptional precision and accuracy, enabling the production of components with tight tolerances. This makes it ideal for applications where even the smallest deviation can impact performance, such as in the aerospace, medical, and automotive industries.
Consistency And Repeatability
Once programmed, CNC milling machines can produce identical parts repeatedly with no loss of quality, whilst also preventing human error in altering the quality between parts. This ensures consistency across production runs, whether you're manufacturing a single prototype or thousands of components.
Versatility
CNC milling is capable of handling a wide variety of materials, including metals like steel, stainless steel, aluminium, and brass, as well as plastics and composites. This versatility allows manufacturers to cater to different industries and customise parts to meet unique requirements.
Complex Geometries
Thanks to advanced CNC milling machines and the power of our CAD/CAM programming software, intricate and complex designs can be machined with ease. Features like internal cavities, sweeping contours, and undercuts are achievable without the need for multiple setups or additional tooling.
Integration With CAD/CAM
CNC milling can be programmed directly on the CNC machine, however, this can lead to a lot of manufacturing time lost when the machine is being programmed before a part can be made. Our software, which integrates with CAD/CAM software and CNC machines, enables precise control over every aspect of the machining process and allows parts to be programmed offline (away from the CNC machine), this allows components to be programmed on a sperate computer ahead of time.
Our CNC Milling Machines
CNC milling is one of our core strengths, backed by decades of experience and an unwavering commitment to precision and quality. We have a large array of 15 modern CNC machines, enabling us to machine items up to 2500mm long and 1000mm wide as well as all sizes in between; which allows us to produce a wide range of components, from highly intricate prototypes to larger production runs. Our machines are equipped to handle a variety of materials, as mentioned above, ensuring versatility across industries. Using our CAD/CAM software we are able to process all popular types of 3D models such as IGS, STP, DWG, VDA, sldprt, SAT, DXF.
2 x DNM400 CNC 3 axis machines – 12,000 RPM spindle speed, Bed size, 520mm X axis, 400mm Y Axis, 480mm Z Axis
3 x DNM650 CNC 3 axis machines – 12,000 RPM spindle speed, Bed size, 1270mm X axis, 670mm Y Axis, 625mm Z Axis. We also have Nikken 4 and 5 axis for these machines.
1 x Dugard HD2210 3 axis machine - 6,000 RPM spindle speed, Bed size, 2200mm X axis, 1000mm Y Axis, 900mm Z Axis
4 x DNM4500 CNC 3 axis machines – 12,000 RPM spindle speed, Bed size, 800mm X axis, 450mm Y Axis, 510mm Z Axis
1 x DNM 350/5AX CNC 5 axis machines – 12,000 RPM spindle speed, Bed size, 400mm X axis, 655mm Y Axis, 500mm Z Axis.
1 x Correa CF22/25 3 axis machine with rotary head - 2,500 RPM spindle speed, Bed size, 2500mm X axis, 800mm Y Axis, 800mm Z Axis
Why Choose Us?
Our skilled team of engineers combines technical expertise with a customer-focused approach, ensuring that every project meets or exceeds expectations. Our ISO 9001 certification underscores our dedication to maintaining the highest standards of quality and consistency. By running a shift system, we maximise productivity and flexibility, enabling us to accommodate tight deadlines and adapt to the specific needs of our customers.
Whether it’s a complex one-off part or a large batch of components, JR Gilbert Engineering delivers precision machining solutions that our customers can rely on. Our proven track record with bespoke machine builders and various industries demonstrates our ability to tackle even the most demanding CNC milling projects.
We aim to simplify your supply chain by offering a complete solution for your component needs. Beyond precision machining, we can manage all finishing processes for your parts, including anodising, hardening, powder coating, wet painting, zinc plating, galvanising, SurTec coating, PTFE coating, and many more. By coordinating these finishing services on your behalf, we save you the time and hassle of dealing with multiple suppliers. This streamlined approach not only ensures consistent quality but also reduces lead times and simplifies logistics, allowing you to focus on your core operations with confidence that your components will arrive finished and ready to use.
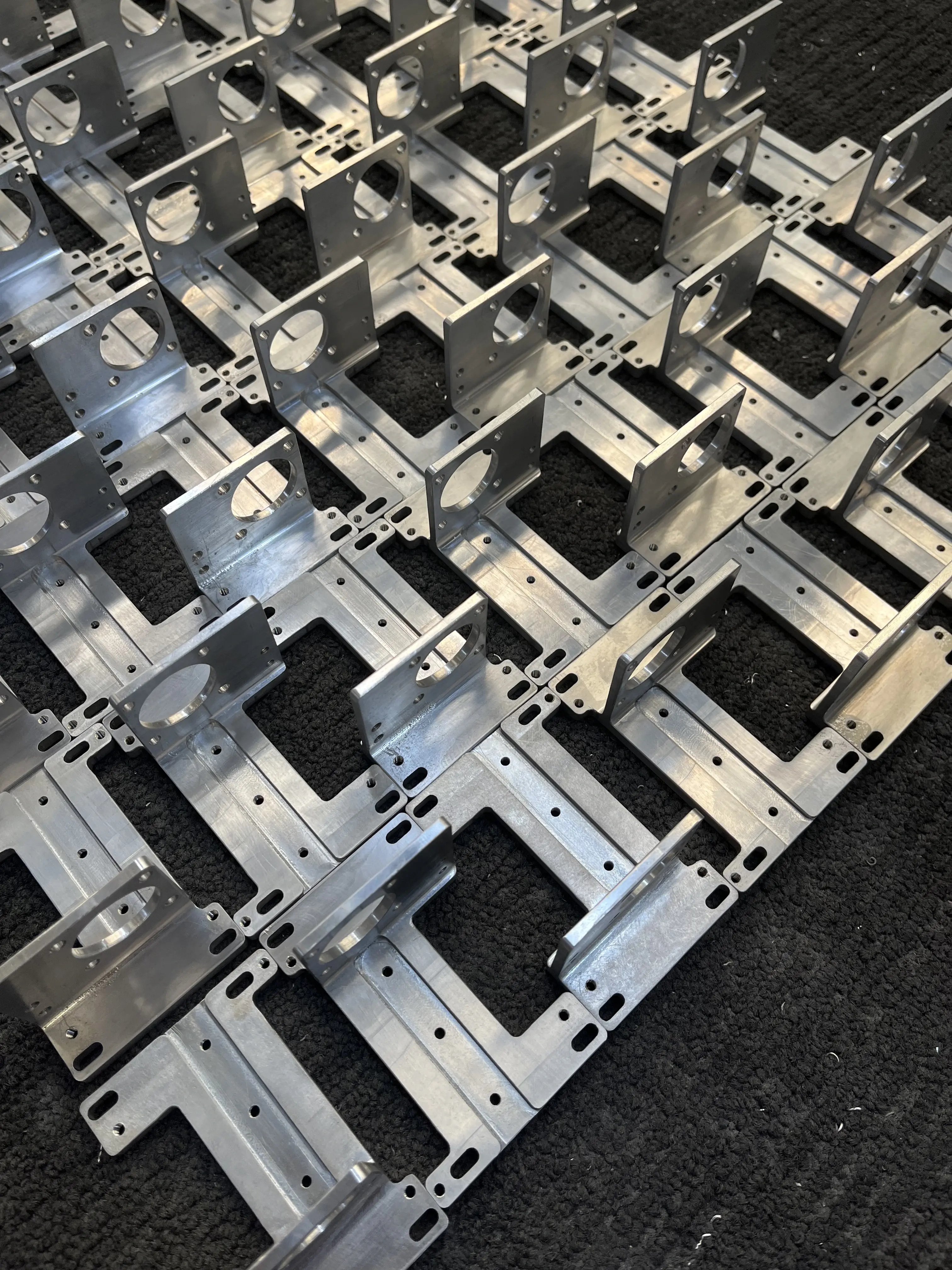
Request A Quote Today
Tired of long wait times and rigid minimum order requirements?
We understand the challenges you face, and we’re here to help. With fast delivery within 2-4 weeks, flexible quantities, and competitive pricing, we provide custom solutions that fit your needs.
Request your personalised quote today and experience hassle-free service.
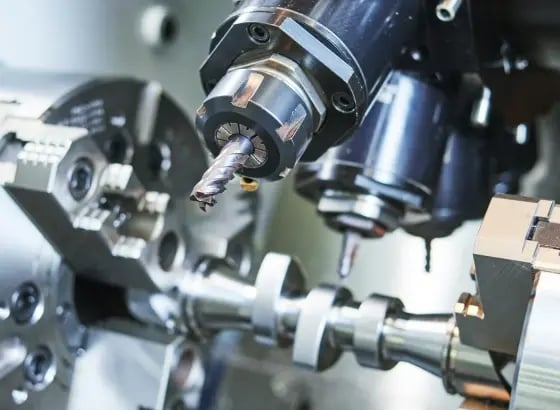
From Our Blog
Stay up to date with what is new in our industry, learn more about the upcoming products and events.

Advanced Precision CNC Machining Capabilities: What’s Driving The Future?
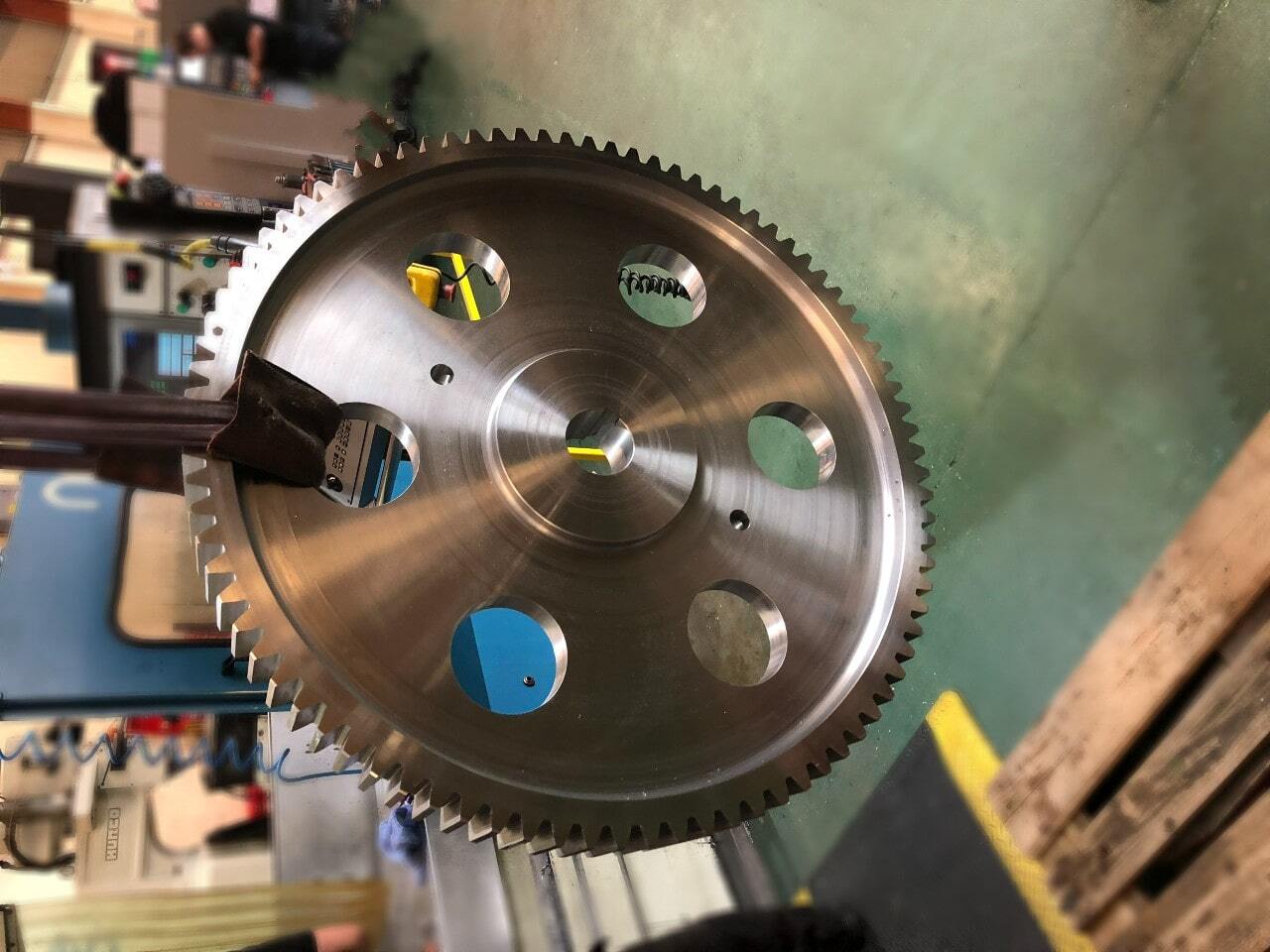
How To Avoid Faulty Custom Machine Parts And Reduce Delays
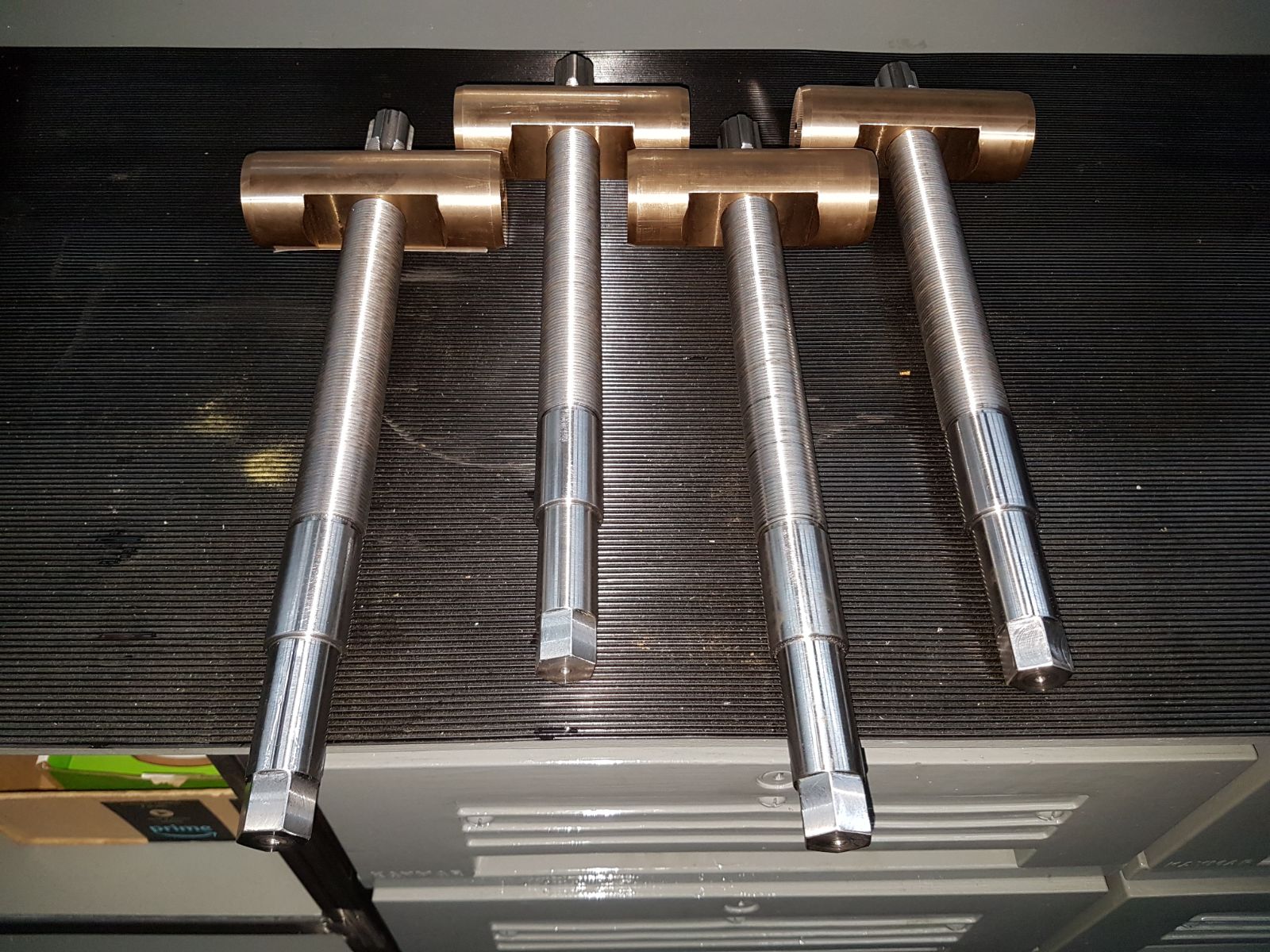
5 Ordering Practices That Help Ensure Consistent Quality of CNC Machined Parts
Quality Accreditations
Providing parts to required specifications combined with a first class service are principal values at Gilbert Engineering. We use quality control measures within our inspection department, as well as calibrated precision testing equipment to ensure that we meet the exact standards required.
Our Quality Management System is accredited by the United Register of Systems: ISO9001:2015.
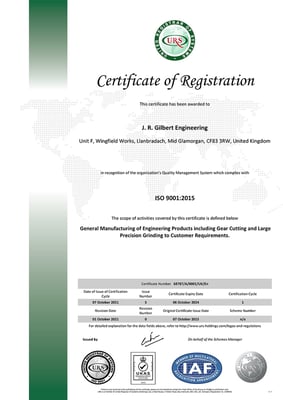
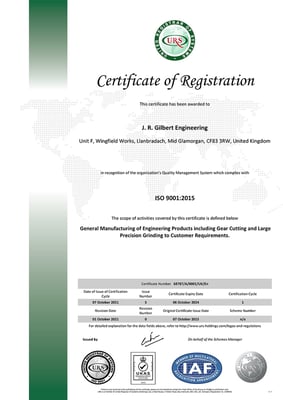